Temperature sensors for monitoring heat pumps
I have been using
OpenEnergyMonitor.org energy monitors with heat pumps for a few years now and thought I should briefly share my experience. This covers the practical side of temperature sensors, and is based on my experience.
(If you just want advice about fitting temperatures sensors onto pipes, skip further down the page)
Introduction
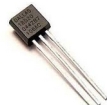
They actually have 3 connections; 0v, 5v and signal. Since each sensor has its own unique i.d. code, multiple sensors are simply connected into the same 3 terminals on the monitor device.
They are mostly bought ‘encapsulated’ in a shiny stainless sensor end all ready with a cable.
The great advantage of these digital sensors is that there are no errors due to cabling. Phone extension cable can be good enough. Thermistor sensors (variable resistance, as PT100) rely on a specific cable resistance and furthermore some sensors could ‘drift’ out of calibration. A further advantage of digital sensors is that they do not in themselves generate heat. They can therefore be used in still air with good accuracy.
If several sensors are strapped together (with an elastic band) and tested in a thermos flask over a few hours, most seem to read within 0.2 degrees C of each other. If you have say 6 sensors, you can chose those that agree most for the most important sensing (e.g. flow and return). Anyhow, these sensors are perfectly accurate enough for this type of monitoring, and there is comfort in knowing that if you are seeing 35.2C (for example) on a graph, then that sensor tip must be at 35.2 +/-, with a small error margin of say 0.15 degrees. This is because the digital signal is generated inside the sensor.
What to measure on a heat pump?
Typical temperature measurement could include the following:
Ground source
Water flow and water return from heat pump (hot side)
Ground collector glycol inlet and outlet from heat pump (cold side)
Outside (ambient) air temperature.
Hot water cylinder temperature, and at least one room temperature.
Air source
Water flow and water return from heat pump (hot side)
Outside (ambient) air temperature and air-off (cooled air leaving heat pump)
Hot water cylinder temperature, and at least one room temperature.
For either of the above there could be a buffer cylinder involved in the design, therefore the flow and return from buffer cylinder to emitter (e.g. underfloor or radiators) may need to be monitored.
There may also be mixing valves (sometimes unnecessary mixing valves) on underfloor manifolds. These may also need monitoring.
For more detailed analysis, the refrigerant internals of the heat pump can be monitored. These may include discharge, suction and liquid temperatures. This is however a little intrusive, and could affect the warranty. It may be necessary to discuss this with the system installers.
Measuring air and liquids
Air
Measuring internal air temperature is relatively straight forward, but sensors must be positioned away from any source of heat or radiation source. Sunlight and close-by appliances and even lighting can greatly affect readings.
The general rule for outside air measurement is to keep the sensor well away from sunshine, or areas that get sunshine. The sensor can also drop below the air temperature if it can ‘see’ a clear sky. A small polystyrene roof is a good shield protection from positive or ‘negative’ radiation (i.e. when radiation from sensor is greater than its surroundings). It is also necessary to keep the sensor dry, unless you purposefully wish to cover it with a wet ‘sock’ to record Wet Bulb Temperature. There is a lot of information available about this relating to weather stations.
Liquids
Most heat pump monitoring involves the temperature measurement of water and liquids flowing in the pipes.
For very high accuracy results, as required by heat meter devices, an immersion pocket is required. (Heat Meters measure the difference between two sensors, so both must be very accurate)
The pocket usually involves a ‘tee’ fitting and a hollow pocket that is completely surrounded by the liquid. The sensor is inserted into the pocket.
An easier and cheaper method is to fix the sensor to the outside of a metal pipe. This method is used in all heat pumps for their on-board sensing.
Any sensor that is outside the liquid can be affected by the temperature of the surrounding air, but the error in the reading can be negligible if the sensor is mounted correctly.
There are various methods as follows-
1) Sensor strapped to metal pipe or metal fitting
2) Sensor inserted in surface pocket (a pipe soldered to the pipe’s surface)
This shows 10mm pipes that have been soft-soldered to copper fittings. Due to the high conductivity of copper, the temperature of the inside of the small pipe is almost exactly the same as the temperature of the liquid inside the pipe. After insulating (lagging) this pipe, the accuracy of the sensor inserted inside the small pipe should be excellent. Ideally the pocket internal diameter is close to the sensor diameter. Conductive paste should be used before inserting the sensor
It is a good idea to fit several pockets like this in the right places during installation. Obviously the pipe must be empty.
Many heat pump manufacturers solder pipes on the outside of water or refrigerant pipes so that their sensor probes can easily be inserted to give accurate measurement
Strapping a sensor to a pipe (or a pipe fitting)Whilst not as good as surrounding the sensor with a conductive copper pocket, it is possible to simply strap the sensor to a pipe. Strapping using a copper strap (as used in refrigeration) , or copper wire, will give better results.
The following shows one simple method.
Copper or brass conduct heat well. The temperature difference between the inside of the pipe and the outside is tiny, so always fit sensors onto metals. Plastic pipes are poor thermal conductors, so the effect of surrounding air can affect the sensor temperature. Furthermore, if the pipe is changing in temperature, the sensor may ‘lag’ in time behind. i.e. it will respond very slowly to temperature changes. This may or may not be a problem.
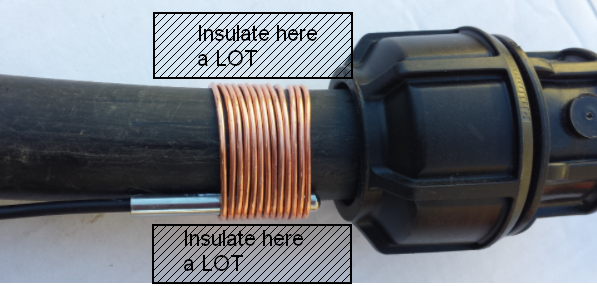
This is not the best position for a sensor since there is 3mm of plastic between the liquid inside and the probe, however, the copper wire strap is making the best of a bad job. Heat will conduct along the copper. There is a lot of copper in contact with the plastic, and this will conduct and will transfer heat to/from the ‘surrounded’ probe. If this is insulated well on the outside, it may give good-enough results for ground source comparisons. Time response may be a little slow, which may not necessarily bad. Fitting the probe onto a metal fitting is a far far better bet.
Hi John, very interesting and helpful.
I have Daikin feeding both CH and DHW, plus a buffer tank. There is a 3 way Y valve to switch between CH and DHW based on the schedule. I’m guessing in this set up, there is no point measuring CH / DHW flow/return rates separately, but rather a single flow/return on the HP side before the 3-way switch?
Any views on what to monitor viz the buffer tank, if anything?
Thanks!
Yes, I would tend to suggest you can simply monitor the flow and return before the 3-way valve. i.e. the flow and return from the heat pump. Next important thing to measure would be the flow and return to the heating system. by looking at the HP flow return and the buffer outlet flow and return, you can assess how much the buffer tank is ‘diluting’ the output from the heat pump. e.g. if you need say 40C to radiators on the coldest days, then the flow at the heat pump should ideally be only a few degrees warmer than 40C
A trick we use in temperature monitoring for cryogenic sensors, where heat conduction though interfaces is almost negligible, is to wrap the sensor /wires/ around the article being measured. This relies on the fact that the conduction through the wire directly to the sensor element will probably be the highest conductivity route. In fact it can be so good that the sensor itself often doesn’t need to be attached!
John
I just started looking at setting up a heat pump monitor using the Open Energy Monitor system. My heat pump is a VRF air to air Mitsubishi and I am wondering how best to set up measuring so that I can get actual COP data.
Thanks
Its very hard to measure heat with air because airflow measurement is only very approximate. The only accurate comparison I know would be to put an electric element in the air flow, and do comparative tests. You can measure electric consumption and temperatures. This is accurate if the air-out temperature is mixed and uniform. Assume electric element has COP of 1.
Bear in mind that the air flow will change depending on the temperatures in the fined heat-exchanger, so, ideally compare rise across electric and HP at the same time. Good luck with it.. well done for having a go.. most people give up.
There is another way of knowing the heat quantity by looking at the refrigeration pressures and temperatures. This is quite complicated and probably only done well by the specific equipment manufacturers.
Thanks John. As a layman, I would like to have a "how to" guide that would show me where best to place sensors in order to have a good view of the current state of the system, including those areas that might indicate problems in the offing. Some generic heat pump diagrams would be useful: a diagram to show sensors required and their positions if one wants to monitor health of the heat pump; a diagram to show sensors required and their positions if one wants to monitor an ASHP-controlled UFH system, etc.
Hello Anon,
I would generally put sensors inside the house (its more stable air temperature environment). There should be little loss in temperature (or watts) between the heat pump and the cylinders / radiators, so position may be more to do with what is practical. Its actually a fairer test to sense near the point of use so that losses are accounted for. If you have plastic pipes, you will need to find a metal fitting to put the sensors onto – a 'tee' is favorite.
Re ASHP, most units (e.g. Ecodan) have a temperature sensor by the back grill where air is sucked in. You could put one sensor here. You can also tie one at the front where the air flow is high. Its interesting to see how this tempeure drops (relative to inlet air) as the coil freezes and the air gets constricted by the ice.
Re a position for tell-tale senor within the heat pump .. Yes, the small discharge pipe that comes from the compressor might be worth sensing. You might find it hard to make sense of the values, but in general, relative high temperatures are bad here. To put it another way, if there is refrigerant loss or general poor performance, this sensor will be higher than a more healthy heat pump. Maybe I need to write a bit more about this? Maybe we need some generic heat pump diagrams on OEM site?
Thanks John, this is very useful for me as an enthusiastic layman. A couple of questions: I have an ASHP outside which provides heat for my UFH system. Where is the best place for the sensors you recommend? For example:
a) for the water and flow and return, is it better to have the sensors at the ASHP, where the pipes enter the building, or close to the point of use (hot water tank or underfloor heating manifold).
b) air-off (cooled air leaving heat pump) – sensor inside the ASHP unit in front of the fan?
Is there something within the ASHP that can be monitored to give an early warning signal of potential problems?
Do you have an annotated picture to illustrate where various sensors are best placed?