To my mind, the whole point of having a heat pump is to save energy, so it somewhat jars with me when I see one aspect of a system that is not in-line with that aim.
A heat pump always stores Domestic Hot Water (DHW) in a cylinder. The Cylinder is, we hope, sized and optimised for heat pump use so that the COP (and lowest running cost) is the best-we-can-get. This detail should be taken care of by the manufacturers and designers.
The detail of distributing the water to the taps is however often done using rule-of-thumb and the installer’s past experience. Energy-efficiency is often low down on the priority list, so may be given little thought.
Hot water must of course be available at a sufficiently high flow-rate, this may lead to choosing a large-bore supply pipe. However, this large bore pipe holds a lot of water, so when a tap is turned on, there can be a long wait before the tap runs hot. After the tap is turned off, the heat from this volume of hot water left in the pipe is slowly lost. This is not good for energy-efficiency and low running costs. This may in-part usefully heat the house, but often it is simply a waste. It is certainly a waste of water. I recently came across a pipe run that took such a long torturous long route that I filled a whole sink before the tap stared to run warm!
For sake of energy-efficiency, the distributions to taps should be;
- The smallest diameter to give adequate flow rate
- As short as possible – the most direct route.
Normally, a single ‘main artery’ is taken from the cylinder, and run to taps in turn. This distribution pipe will normally start big and, as each ‘tee’ off to a tap, it will at some point reduce in diameter. Furthermore, if several taps are on at the same time, then one flow may affect the other. E.g. the pipe needs to be big enough in diameter to maintain a good steady flow-rate for a shower.
The choice of pipe size is often a dilemma, so playing-safe and choosing larger pipes would at least safeguard against an inadequate pipe run. This would however tend to go against saving energy.
Running separate pipes from the cylinder.
The pipe run to the bath is usually large diameter. This is where the fastest flow may be needed so that the bath fills quickly. However, a bath is not used very frequently, so the losses as described above may not be as great here as envisaged. Kitchen sinks however tend to be used many times over the day, so total losses of heat and water could be high.
The worst scenario could be a kitchen sink at the end of a large long pipe run via a bath.
A solution to this could be to run dedicated pipes directly to sinks.
Here are some suggestions for new-builds
- Position the cylinder as close to the taps that are most frequently used (e.g. the kitchen sink). Ideally find a central location to all taps.
- Early on in the build, organise the most direct pipe run routes from the top of the cylinder to the sinks. (the ceiling is often shorter than running in the floor)
- Decide the best configuration, e.g. some sinks can share, others may benefit from their own dedicated supply pipe.
- Identify the most suitable diameter of pipe.
- Insulate frequently-used pipes, BUT this may give limited advantage since it may simply take longer to lose all the heat in the pipe.
Pumped secondary return loop
Hotels and large houses often adopted a pumped circulation loop so that the taps run hot almost immediately. This saves water and is convenient to use, however, the hot loop can waste a lot of energy, even if well-insulated. I would try to avoid a pumped loop if possible. It may be better to have point-of-use direct electric heaters, than to have a pumped loop that is always wasting heat.
Copper v plastic
There is a bit of a myth that suggests that plastic pipe is ‘smoother’ than copper. The most important factor for flow-rate is the actual bore size. The wall material makes little difference. However, plastic can very easily be bent with sweeps, these are better than straight pipes with tight bends. In this sense, plastic can be ‘smoother’.
Anyhow, the difference between copper and plastic is quite dramatic due to its internal bore.
It is very important to allow for the internal pipe sizes, and it is possible to use a combination of the two, e.g. run plastic through the middle of joists if it’s possible, but use long straight runs of copper along a wall.
I have put two charts at the bottom of the page here http://heatpumps.co.uk/types-of-heat-pump/domestic-hot-water-dhw/
There are figures here to give a rough idea of what sizes might work. It is surprising how much more restrictive 15mm plastic is compared to 15mm copper. This info goes along with a disclaimer since it can be hard to know all the factors involved in a system. I am a great believer in getting a sample of pipe in a coil and doing a test on site with a bucket.
You can also play with this great little pressure-drop calculator for theoretical pipe sizes
What could go wrong?
I have successfully run a kitchen sink via a 10mm plastic pipe. The bore is only 6.7mm which is less than the diameter of a pencil. I had no noise problem at all. In general, more noise would come from part-open valve or tap than would come from a smooth pipe. Remember to clip the pipe well to stop any annoying clonking that can occur with any pipe when a tap is shut-off quickly.
Thank you for all your insights. We are currently having an ASHP installed, with solar PV, and looking forward to seeing how it plays out in our home.
I know the question I have is not related to tap outlets, but I was wondering if you had any advice on whether you think keeping the hot water function constantly on is cheaper than than turning it on when you need hot water? Our installers say it is cheaper to keep it on constant, whereas we would just give it a boost when we needed it.
Any insight on this would be hugely appreciated.
When the cylinder is cold, and starts heating, the COP is very high, as the cylinder gets hotter and hotter, the COP reduces. It’s the last top-up that has the lowest COP.
Obviously, you need to keep the cylinder hot enough, so the trick is to allow it to cool where possible. Timing it off overnight would be sensible, and if you are very frugal,time it off mid morning and/or mid afternoon… this might save a tiny bit.
If you have a Legionella cycle enabled, you should make sure it happens when DHW is enabled (timed on). Some models, very annoyingly, use the electric immersion for this rather than using the heat pump all it can, then finishing off with the immersion.
Firstly can I say a big thank you for your excellent book and web site – your information has been really helpful to me and many others I am sure.
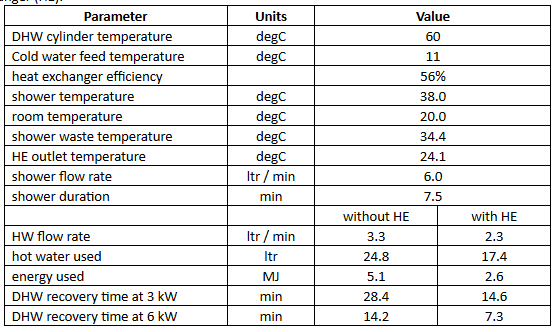
I am designing the DHW system for a low-energy retrofit of my home, and I would like to ask your advice about the choice of cylinder. I would also be very grateful if you would check what I have overlooked in my thinking about this system.
I have looked at several ASHPs and chosen the Stiebel Eltron WPL-A 05, which gives 3 to 6 kW output with good efficiency and can give a flow temperature of 75 degC. After the retrofit, my worst-case space heating load will be 2.6 kW so this ASHP should be big enough. Suppliers I have spoken to proposed a DHW cylinder size of 250 ltr, but this seems way too big to me. To minimise heat losses in the DHW system I want to use a much smaller cylinder, and the calculations below show 90 ltr should be big enough for my needs.
I have three showers and no bath, with a PowerPipe heat exchanger that recovers around 50% of the heat in the shower waste water. The PowerPipe pre-heats the cold feed to each shower, reducing the amount of hot water used. It also pre-heats the cold feed to the cylinder, so re-heating takes less energy. The table below shows the effect of one shower on the DHW system, with and without the heat exchanger (HE).
Using the heat exchanger means one shower draws only 20% of the hot water in the cylinder, so I can have 5 showers before the hot water runs out. If the ASHP output is 6 kW, the cylinder temperature drop following one shower can be restored in less time than the shower duration.
The best 90 ltr cylinder I have found so far in my search is the Gledhill IND90, which loses only 32W at 60 degrees. The primary coil area is only 0.59 m^2 – a lot smaller than the 3 m^2 you recommend in your excellent guide to DHW systems, but I think it may be good enough.
From the IND90 data sheet I estimate the primary coil will transfer around 380 W per degree, so the ASHP flow would be 8 degrees above DHW temperature at 3 kW, or 16 degrees at 6 kW. This is not as good as the 5 degrees you suggest, but not awful. I can choose to get a “fair COP” by heating at 3 kW, or accept a lower COP if I need a faster recovery time.
Can you suggest a better choice of cylinder than the Gledhill IND90?
Do you think this system looks reasonable ?
Dear John, I enjoyed your blog post, but must disagree with your dismissal of the secondary hot water circulating system as ‘a waste of heat energy’. Whilst the hotel industry routinely uses this type of system it is for the implied demands of their customer, who generally expects hot water 24 hours per day.
In the domestic environment this approach would be unacceptable from an energy loss (heat and pumping) viewpoint, however there are times, usually in larger domestic dwellings, when a carefully designed secondary circulation system would pay dividends.
The chief driver for this is convenience; that is the occupants want hot water without delay, and without the obvious visible waste while waiting for it to arrive. One way to achieve this is to have low volume pipework and, to achieve the desired flow rates at the taps, higher pressures than those from the traditional open vented system (with a cold water storage tank in the loft). Higher pressures than that of the mains incoming supply are only practically achieveable with additional pumping energy, so we are left with the best compromise to date, the unvented hot water cylinder (the Megaflo and similar).
Heat losses from the smaller distribution pipework when using an unvented cylinder (UVHW) can therefore be reduced when compared to the vented system, but beyond that we can only insulate to reduce the heat losses radiated from the pipework.
On the face of it the secondary circulating system would increase those losses (because the average temperature of the water in the distribution system would be higher), but with careful use of the technology available today these losses can be greatly mitigated.
The use of better controls (of which I detect you are a fan) can achieve this by:
1. Timing the secondary circulator to run only when persons are on the premises (PIR detectors, etc).
2. Intelligently switching-on local inline electric heaters when night-time movement is detected, ie hand rinsing after use of the toilet.
3. Using ‘smart’ controls to detect and predict periods of low occupancy/water use.
4. Geofencing information to augment the above.
To conclude, there will always be a class of persons who will value convenience and comfort over cost. We must make it easier for these people to use their wealth to buy energy saving devices without detriment to their comfort.
Good to hear another point of view. I have only seen bad examples of these loops. For those who use a lot of hot water, I guess a properly done loop could be good.